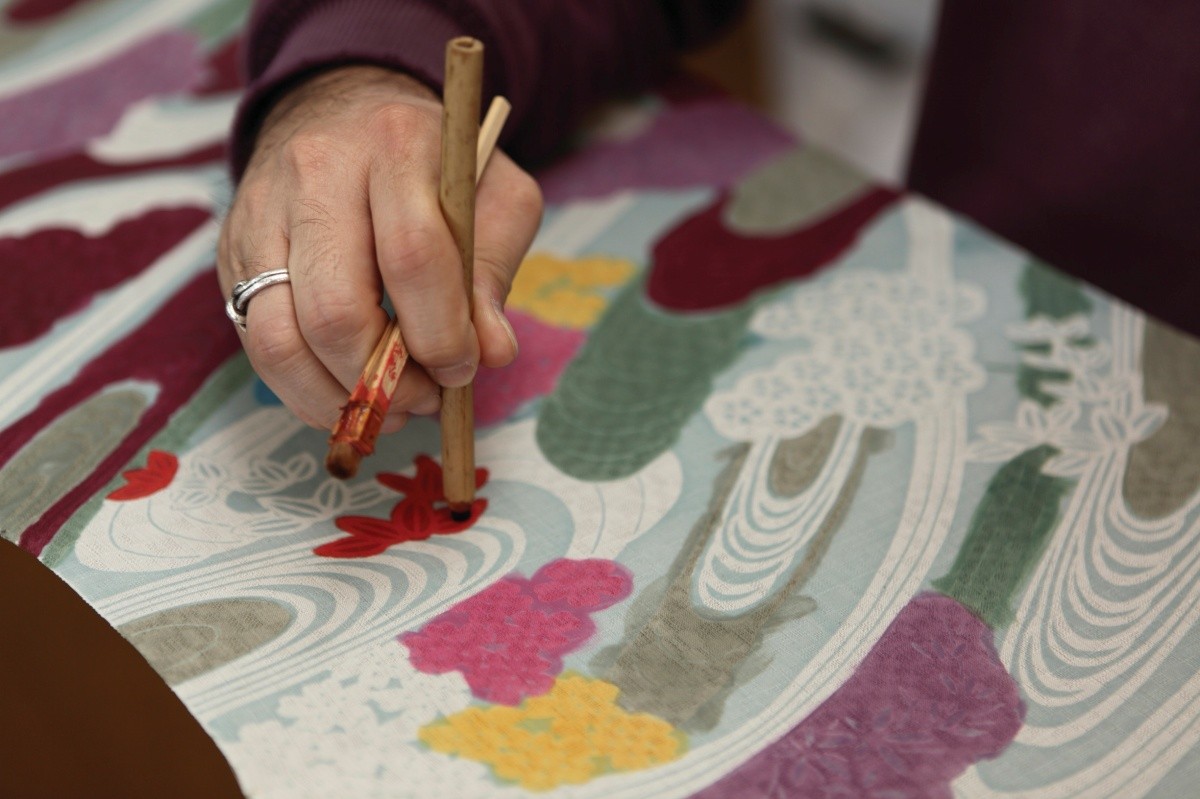
Did you know that the fabric used for making Japanese kimono can be divided into two main types: dyed fabrics and woven textiles? Among these, dyed fabrics have various techniques and classifications based on their colors and patterns, each with its own unique name. This article will introduce the characteristics, history, and types of Japan's dyed fabrics. Let’s embark on a journey to explore the fascinating world of dyed textiles!
* If you purchase or book any of the items featured in this article, a portion of the proceeds may be returned to FUN! JAPAN.
Features of Japanese Dyed Fabrics
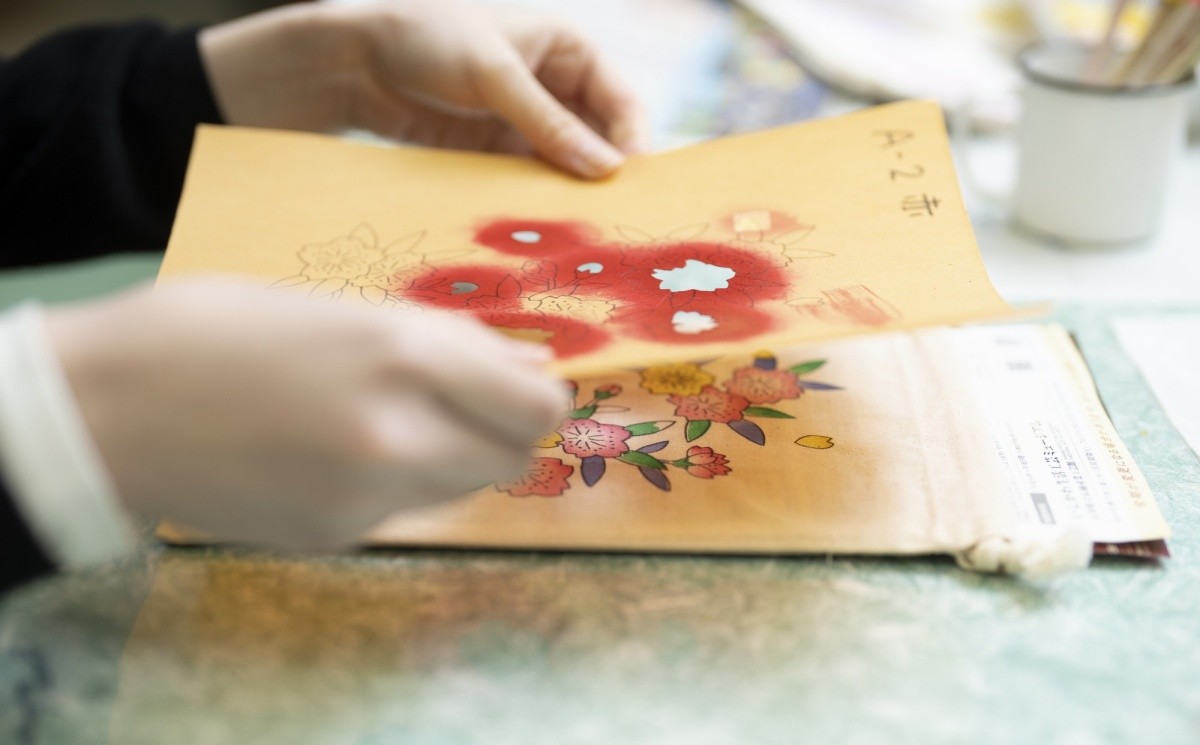
Japanese dyed fabrics and woven textiles are used to make kimono and traditional accessories. Dyed fabrics are also referred to as "some-mono" (dyed items). While both are created using traditional techniques, their primary difference lies in the order of production. For woven textiles, the threads are dyed before being woven. In contrast, dyed fabrics start with a plain white cloth, which is then dyed or patterned. This is why woven textiles are called "pre-dyed" fabrics, while dyed fabrics are known as "post-dyed" fabrics. Moreover, dyed fabrics encompass a variety of techniques and styles, each of which has evolved in tandem with the lifestyles and cultures of its era.
The History of Dyeing in Japan
The history of dyeing in Japan dates back to the Jomon period when natural dyes made from plants and soil were used. During the Nara period, dyeing techniques were introduced from China and the Korean Peninsula, laying the groundwork for modern Japanese dyeing and popularizing techniques such as patterned dyeing.
In the Heian period, Japan's unique "kokufu" culture flourished, leading to the creation of traditional Japanese colors and patterns, along with advancements in dyeing techniques. This era saw the development of cultural practices like assigning specific colors based on social rank or seasons and layering thin garments in coordinated colors, as seen in the twelve-layered ceremonial kimono (juni-hitoe).
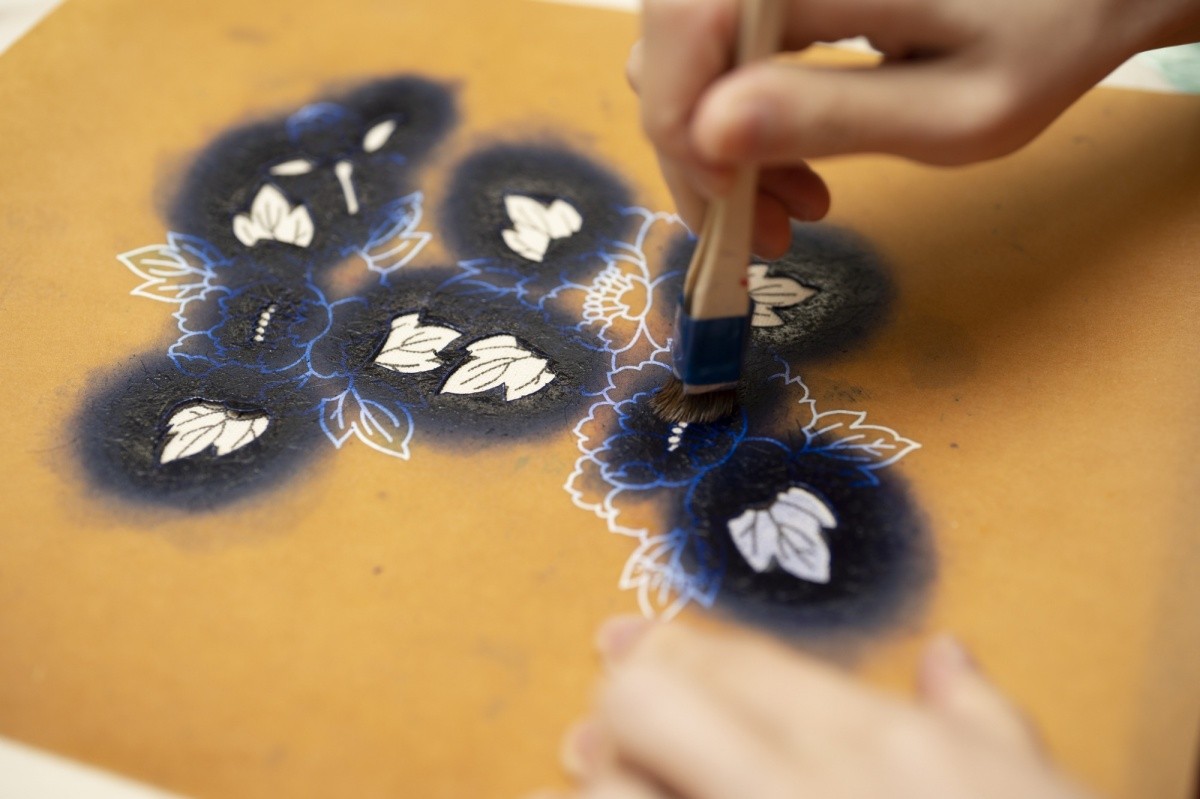
During the Edo period, dyeing techniques improved further, and dyed fabrics became popular even among commoners as a form of stylish fashion. Midway through the Edo period, the vibrant and intricate yuzen dyeing method was developed, enabling artisans to paint vivid designs onto fabrics.
In the Meiji period, chemical dyes from countries like Britain were introduced. These dyes were less costly than natural dyes and offered a stable supply, leading to their widespread use. Over the years, Japan's dyed fabrics have been shaped by the cultures, lifestyles, and technologies of each era and continue to be cherished today.
Techniques of Dyed Fabrics
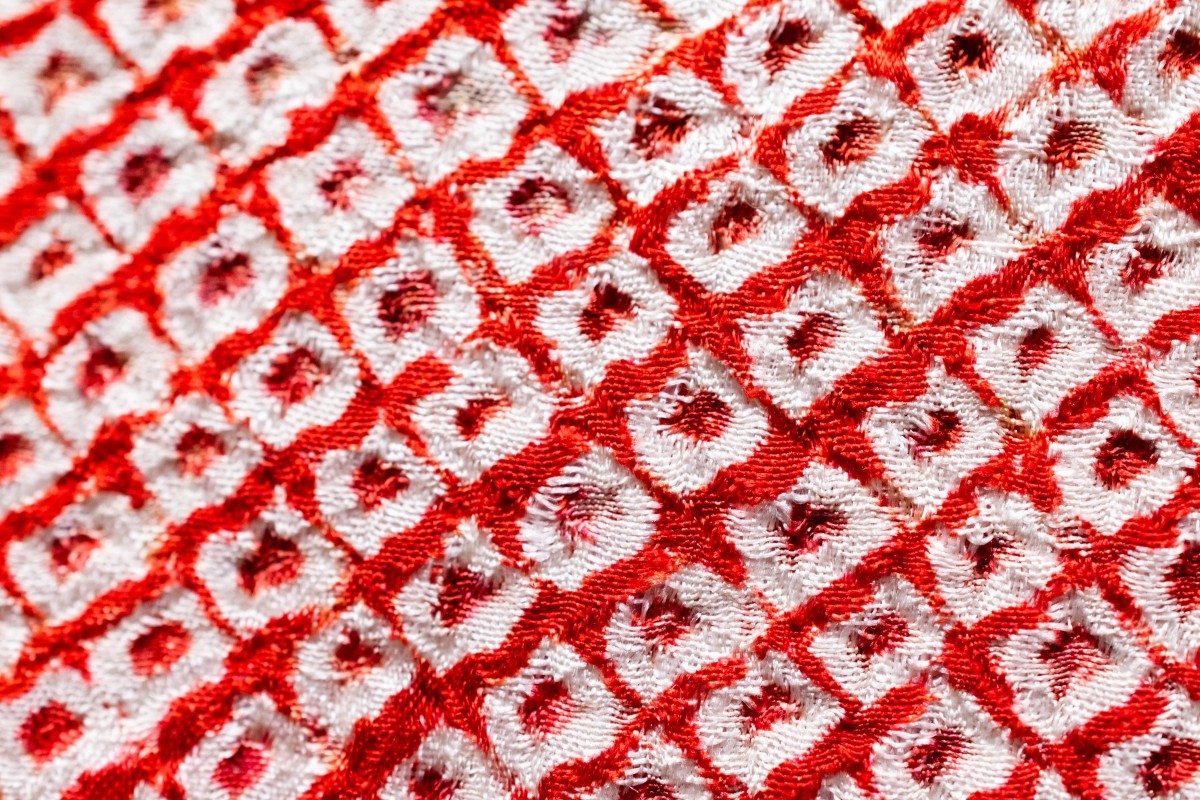
There are various methods for dyeing post-dyed fabrics, but the two most common techniques are immersion dyeing (shinsen) and resist dyeing (nassen). The primary difference lies in whether the dye penetrates through the fabric or only colors the surface. Let’s explore these two techniques.
Immersion Dyeing (Shinsen)
Immersion dyeing is a method where fabric is submerged into a water-soluble dye solution to achieve coloration. When fabric is dipped into the dye without any resist treatment, it results in a solid-colored fabric. However, if certain areas are treated to resist dye, patterns can be created on the fabric. One of the most iconic dyed fabrics using this technique is "shibori" (tie-dye). In shibori, a white fabric is pinched, tied with thread, or folded to create resist areas before being immersed in dye. These resisted sections remain white, forming patterns. Beyond tying with thread, other methods such as stitching or clamping the fabric between boards are also used to create unique designs.
Resist Dyeing (Nassen)
Resist dyeing involves applying dye only to the surface of a plain white fabric. This can be done either by hand-painting directly onto the fabric or by using stencil-dyeing techniques, where patterns are carved into paper stencils, and dyes are brushed onto the fabric through these stencils. Unlike immersion dyeing, which saturates the fabric, resist dyeing only colors the surface fibers. This allows for creative possibilities such as having different patterns or colors on the front and back of the fabric.
Traditional Craft Designated Dyed Fabrics: Immersion Dyeing
Arimatsu Shibori and Narumi Shibori (Arimatsu Shibori/Narumi Shibori)
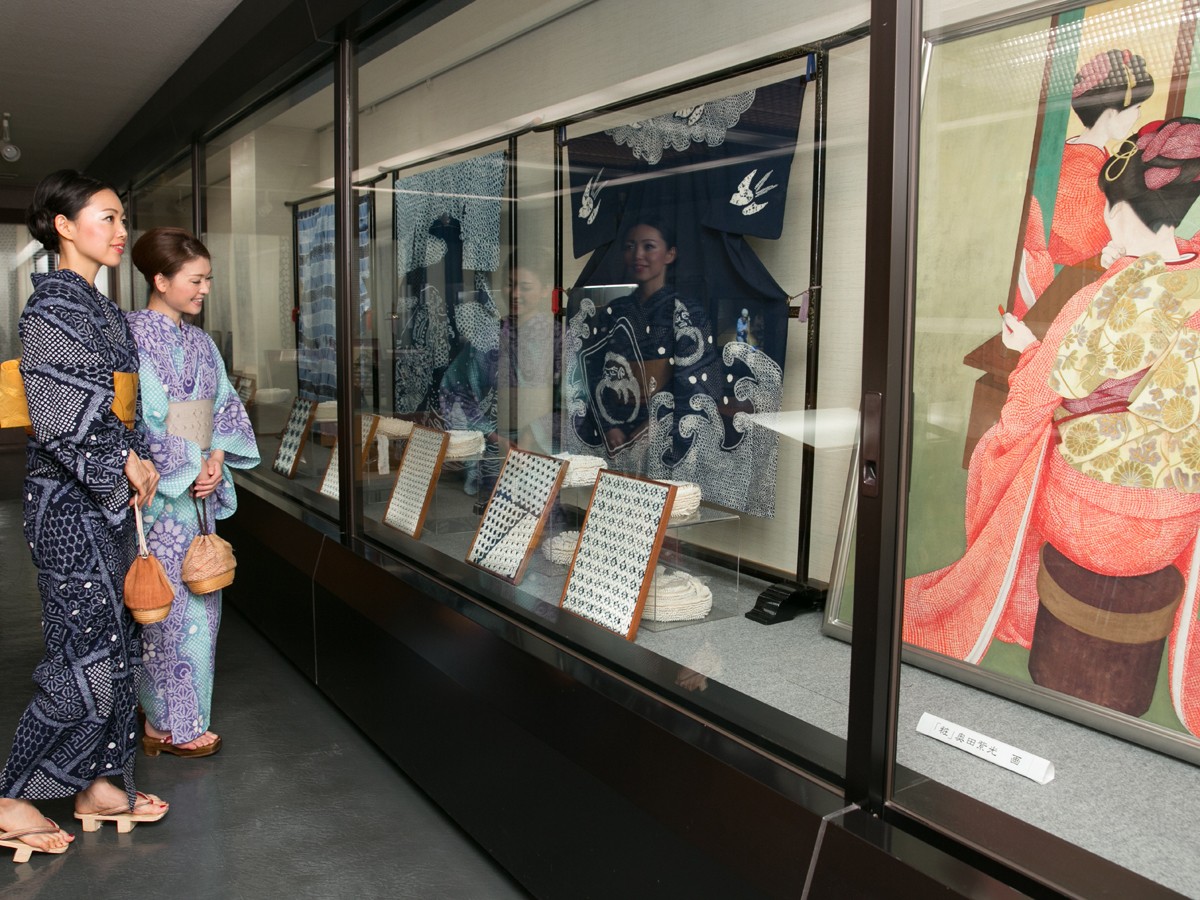
Arimatsu Shibori and Narumi Shibori have been produced around the Midori Ward of Nagoya City in Aichi Prefecture. Techniques such as "kanoko shibori" (fawn-spot tie-dye) and "nui shibori" (stitched tie-dye) encompass around 100 different methods. The depth of color, intricate patterns, and handmade texture achieved through these techniques are what make Arimatsu and Narumi Shibori so special.
The origin of these crafts dates back to the early Edo period. Inspired by the tie-dye clothing worn by workers building Nagoya Castle, a local named Shokuro Takeda began creating Arimatsu Shibori by applying tie-dye techniques to hand towels made from Mikawa cotton. Initially, this craft was produced only in the Arimatsu area. However, travelers passing through the nearby Narumi lodging station often bought these tie-dye fabrics as souvenirs, leading to the name Narumi Shibori. Over time, the two names became synonymous, resulting in the joint designation Arimatsu and Narumi Shibori.
👉 Shop for Arimatsu Shibori products (Yahoo! Shopping)
Kyō Kanoko Shibori (Kyoto Kanoko Shibori)
Kyō Kanoko Shibori is a dyeing technique where white fabric is pinched, tied with threads one by one, and dyed to leave parts undyed, creating a pattern. This dyed fabric is produced in Kyoto Prefecture. The technique flourished during the mid-Edo period. The name "Kanoko" (fawn) originates from the resemblance of the patterns to a fawn's spots. There are over 50 types of shibori techniques, and each craftsman specializes in one type.
In Kyō Kanoko Shibori, each small section is tied individually, and for each color used, the dyeing process is repeated. The tiny patterns can be as small as 10–15 dots in just 3.8 cm, with each dot measuring about 2.5 mm. Because of this intricate handcrafting, it takes an extraordinary amount of time to complete a single piece. For example, it may take up to a year and a half to create a fully shibori-dyed kimono (*1) or over two years for a furisode (*2). Additionally, the slight variations in tying due to the handmade process result in unique textures, making no two pieces alike. This uniqueness is part of the charm of Kyō Kanoko Shibori.
*1 Kimono where the entire fabric is dyed using the shibori technique.
*2 A type of kimono with long sleeves, worn as formal attire by young, unmarried women.
👉 Shop Kyō Kanoko Shibori products (Yahoo! Shopping)
Tokyo Mūjizome (Tokyo Plain Dyeing)
Tokyo Mūjizome is the most fundamental dyeing technique, involving dyeing silk fabrics in a single color. However, dyeing 13 meters of fabric evenly without blotches is no easy task. fMūjizome originated in the mid-to-late Edo period when dyers used solid colors such as Edo purple, Edo brown, and indigo. During the Edo period, the government frequently issued "luxury restriction laws" that prohibited the use of extravagant colors. Even so, the people of Edo refused to give up their sense of style. This led to the popularity of Edo's plain dyeing and Kyoto's shibori dyeing. There was even a saying, "Edo purple and Kyoto Kanoko," which symbolized the excellence of Edo's purple dye and Kyoto's shibori dye, reflecting the fashion trends of both regions. The pinnacle of these techniques has been passed down and is preserved in today's Tokyo Mūjizome.
👉 Shop Tokyo Mūjizome products (Yahoo! Shopping)
Traditional Craft Designated Dyed Fabrics: Printing Dyeing
Kyō Yūzen (Kyoto Yūzen)
Kyō Yūzen, produced in Kyoto Prefecture, is a dyeing technique featuring colorful, artistic patterns. It was devised by Miyazaki Yūzensai, a fan-painting artist in the Edo period. Unlike other techniques that dye the fabric before shaping it, Yūzen starts by sewing the fabric into the shape of a kimono. A design is sketched onto the fabric, and paste is applied to the outlines to prevent colors from blending. The dyeing process then uses vibrant, hand-applied dyes.
This intricate process involves numerous steps, each carried out by specialized artisans. However, these steps were not all established simultaneously. Instead, Yūzen evolved by integrating techniques developed over various periods.
After perfecting his dyeing method, Miyazaki Yūzensai taught the technique in Kaga (present-day Ishikawa Prefecture), leading to its spread to Kaga, Edo, and beyond. While each region's Yūzen dyeing has distinct characteristics, one of Kyō Yūzen's hallmarks is its opulence, featuring embroidery and gold or silver leaf. Today, while incorporating modern technologies like chemical dyes and inkjet printing, hand-dyed Yūzen has become increasingly rare and highly valued.
👉 Shop Kyō Yūzen products (Yahoo! Shopping)
Kaga Yūzen
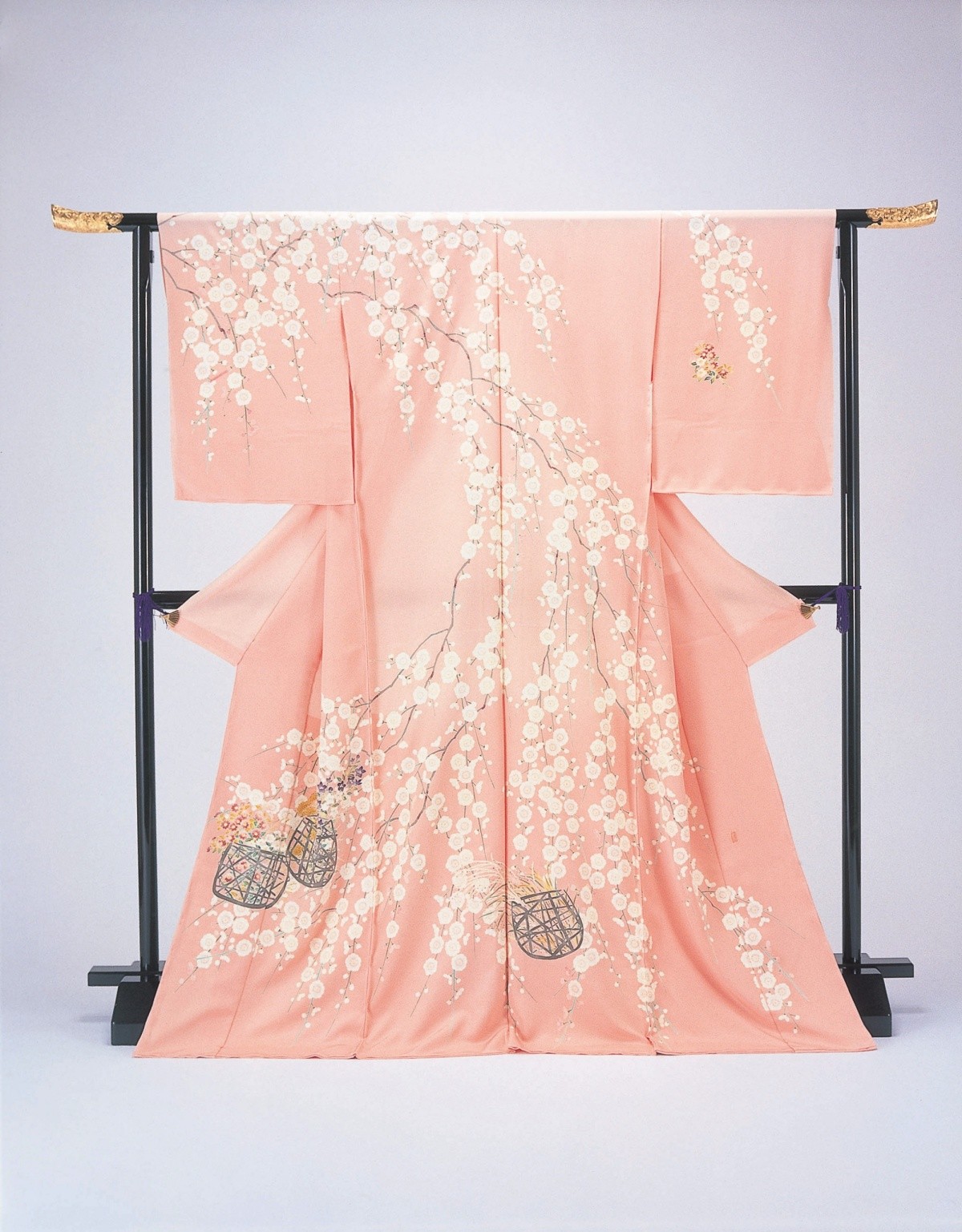
Kaga Yūzen, a dyed fabric originating from Kanazawa City in Ishikawa Prefecture, was developed under the guidance of Miyazaki Yūzensai, the inventor of Yūzen dyeing in Kyoto. Its defining features include the elegant and beautiful patterns created using the "Kaga Gosai" (the Five Kaga Colors): indigo, ochre, grass green, ancient purple, and crimson. Unique to Kaga Yūzen are patterns such as "blurred" effects radiating from the edges towards the center and the depiction of "bug-eaten" leaves. Another distinction from Kyō Yūzen lies in Kaga Yūzen's focus on classical deep red tones and designs inspired by the natural beauty of flowers and plants. Although modern techniques like inkjet printing are now utilized, hand-painted Kaga Yūzen remains committed to traditional methods, preserving its artisanal heritage.
👉 Shop Kaga Yuzen products (Yahoo! Shopping)
Ryūkyū Bingata
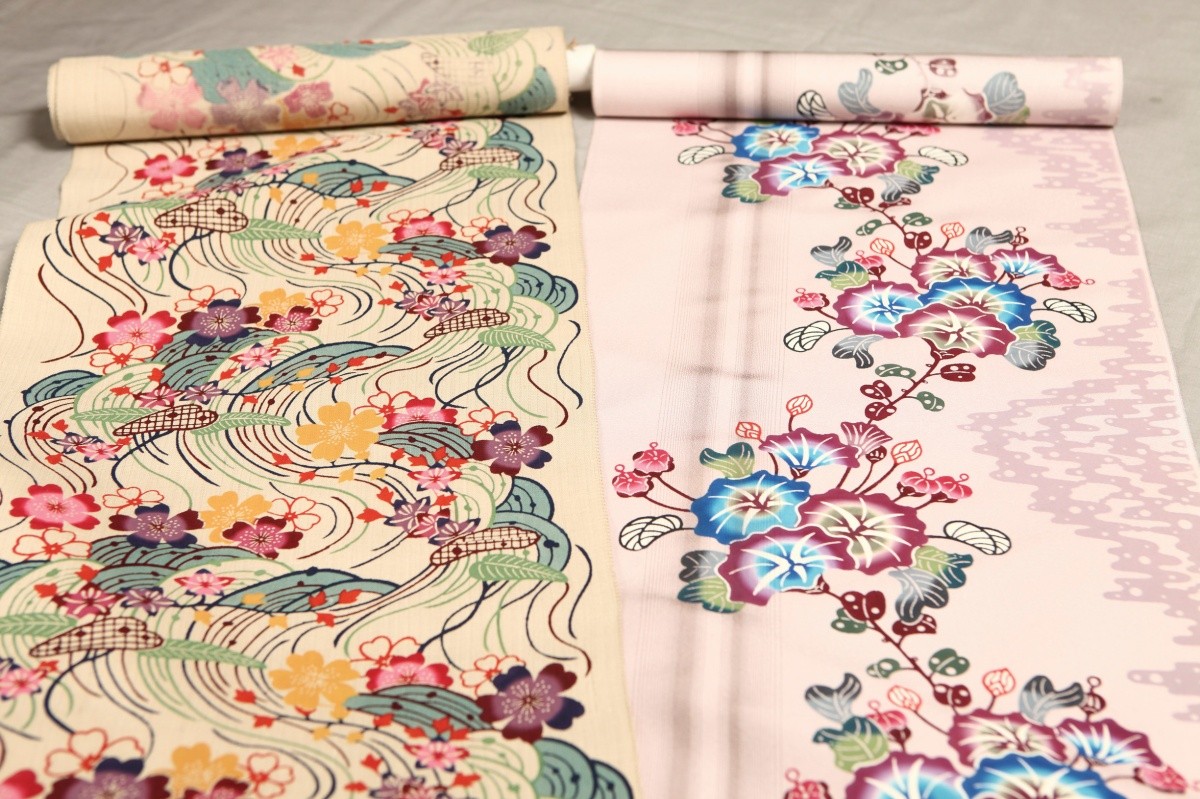
Ryūkyū Bingata, produced around Shuri City in Okinawa Prefecture, traces its origins back to the Ryūkyū Kingdom in the 14th–15th centuries. This dyed fabric encompasses two distinct styles: "Bingata" and "Aigata." Both use stencil dyeing techniques with paper stencils and "tsutsubiki," a method of freehand drawing with paste to create patterns.
Bingata features vivid colors reflecting the tropical climate and was traditionally worn as ceremonial attire by the royal and aristocratic women of the Ryūkyū Kingdom. In contrast, Aigata, which uses only Ryūkyū indigo for dyeing, was used for everyday or indoor garments by the aristocracy and was reserved for elderly commoners.
The legacy of Ryūkyū Bingata has been preserved by two families of the three original dyeing houses that served the Ryūkyū royal court. Thanks to their dedication, the techniques from the Ryūkyū Kingdom have been passed down and shared with wider audiences.
Comments