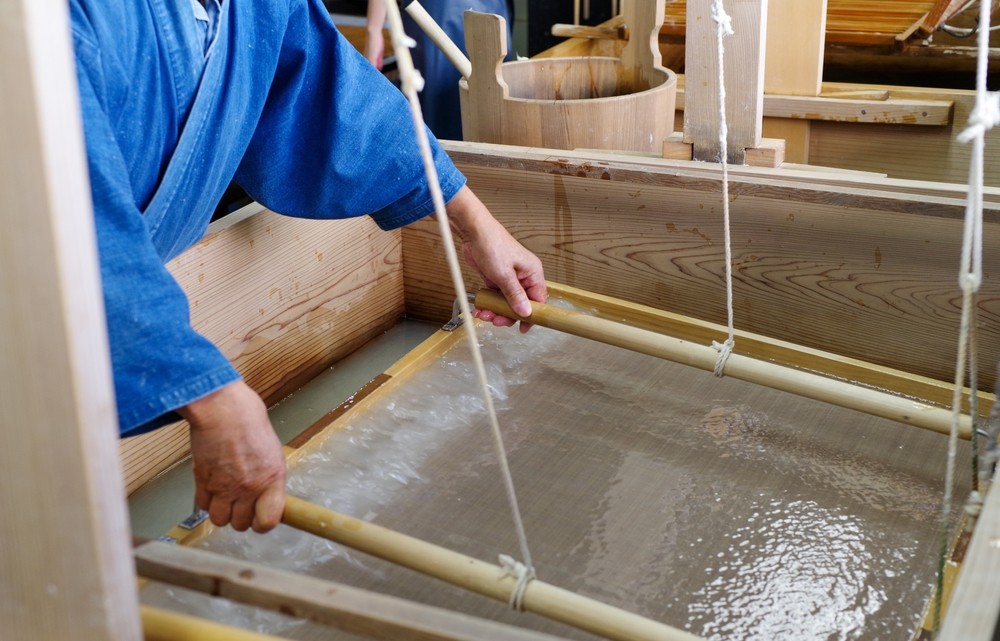
Washi is a traditional craft technique that Japan is proud of, and it has been designated as a UNESCO Intangible Cultural Heritage. Its abundant types and wide range of uses are attracting attention from around the world.
In this article, we introduce the history and types of washi, as well as places where you can actually experience the process of making washi. We have also carefully selected some high-quality products made from washi, so if you are interested, please consider them!
History of Washi
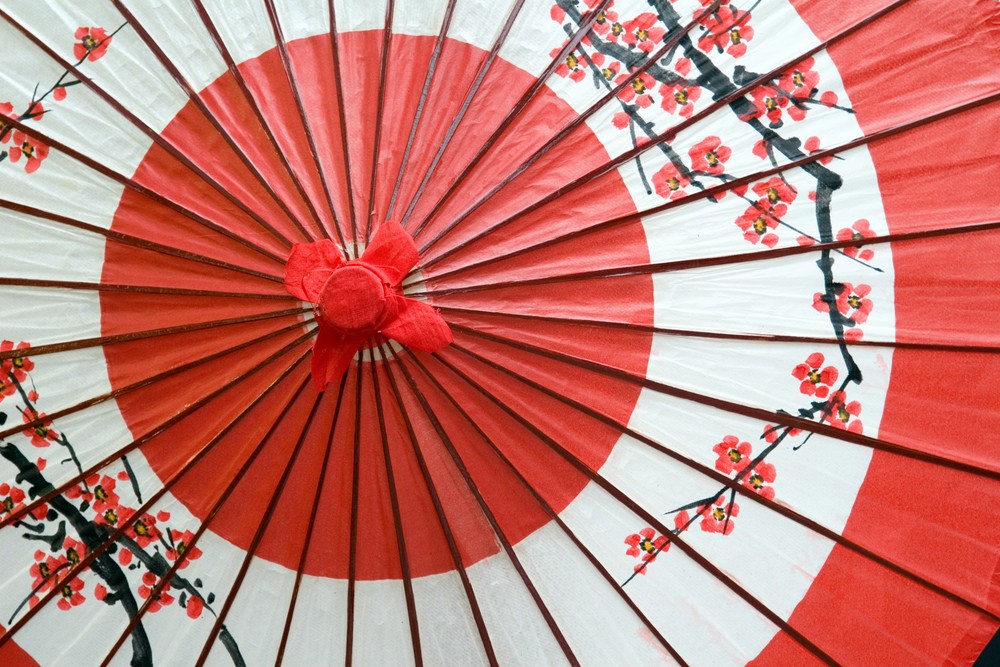
Washi, a material deeply rooted in Japanese aesthetics and traditional culture, is believed to have originated from China. During the Heian period (794-1185), it was popular among the nobility, and from the Kamakura period (1185-1333) onwards, as the political center shifted from the nobility to the samurai, the use of washi also spread in the world of the samurai. Furthermore, during the Edo period (1603-1868), it became widespread among the common people. Items such as Japanese umbrellas and shoji screens are made from washi.
With the spread of Western paper in modern times, washi experienced a temporary decline, but it has been revived due to the reevaluation of traditional culture, and now products that incorporate new technologies and designs are also being produced. In addition, Japanese hand-made washi technology was registered as a UNESCO Intangible Cultural Heritage in 2014, and has gained international recognition.
What are the characteristics of washi? How is it different from Western paper?
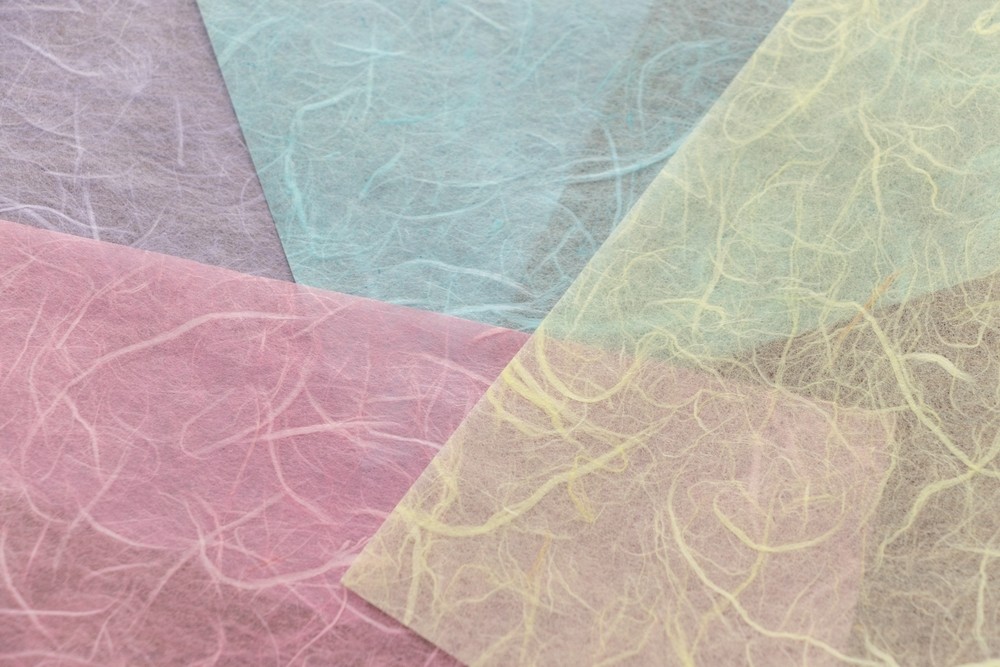
Before the Meiji Restoration, foreign-made paper was not imported into Japan, so there was no distinction between "washi" (Japanese paper) and "yoshi" (Western paper), and the demand was fully met by domestic production. Subsequently, with the promotion of policies such as the civilization and enlightenment, the demand for paper increased significantly, and paper began to be imported from Western countries such as the UK.
Nowadays, washi and yoshi each have their own needs, but what exactly are the differences? To make it easier to compare the two, we have summarized the raw materials, paper quality, fiber characteristics, suitability for long-term storage, etc. in the table below.
Raw Material | Paper Quality | Fiber | Long-term Storage | Mass Production | Price | |
Washi | Kozo, Mitsumata, Gampi | Surface is uneven and rough | Fibers are long and strong | Suitable | Difficult to mass produce | Expensive |
Yoshi | Pulp | Surface is smooth and uniform | Fibers are short and strength is low | Prone to discoloration and deterioration | Easy to mass produce | Cheap |
Types of Washi
There are many types of Japanese paper, and if classified strictly, there are over 1000 types. Let's take a closer look at the charm of the Japanese paper that has made a name for itself as the "Three Great Japanese Papers" and the Japanese paper that has been designated as an intangible cultural heritage.
The Three Great Japanese Papers
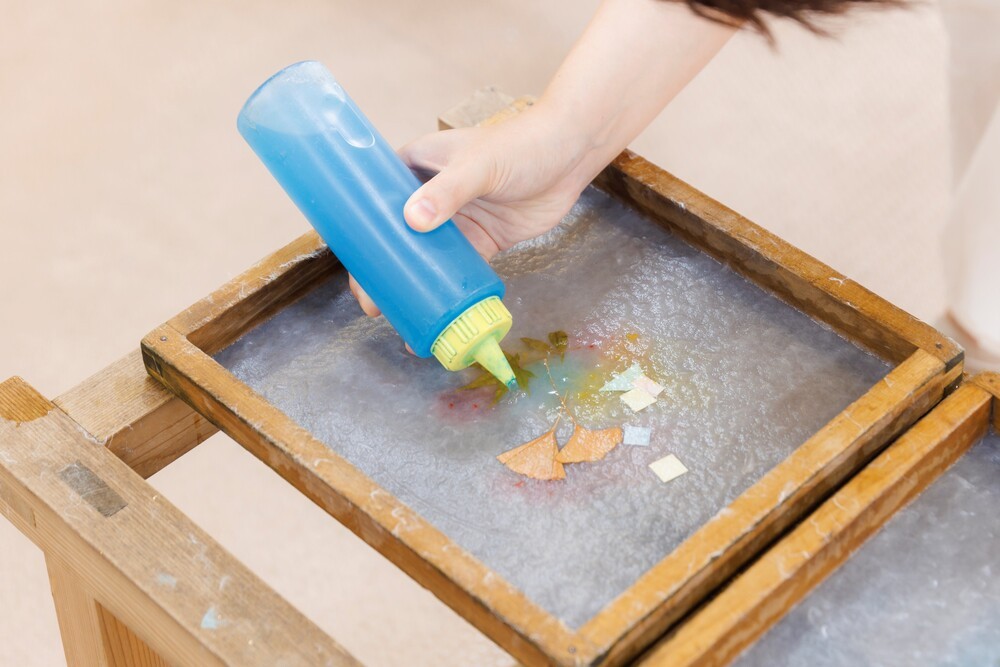
① Echizen Washi (Fukui Prefecture)
- It has been produced for about 1500 years and has the longest history
- The first national currency in Japan, "Dajokan Satsu" (Dajokan Bank Note), was made of Echizen Washi
- It is used as an official paper for securities and graduation certificates
- It is a high-functioning material with antibacterial and deodorant effects, and is also used for space suits
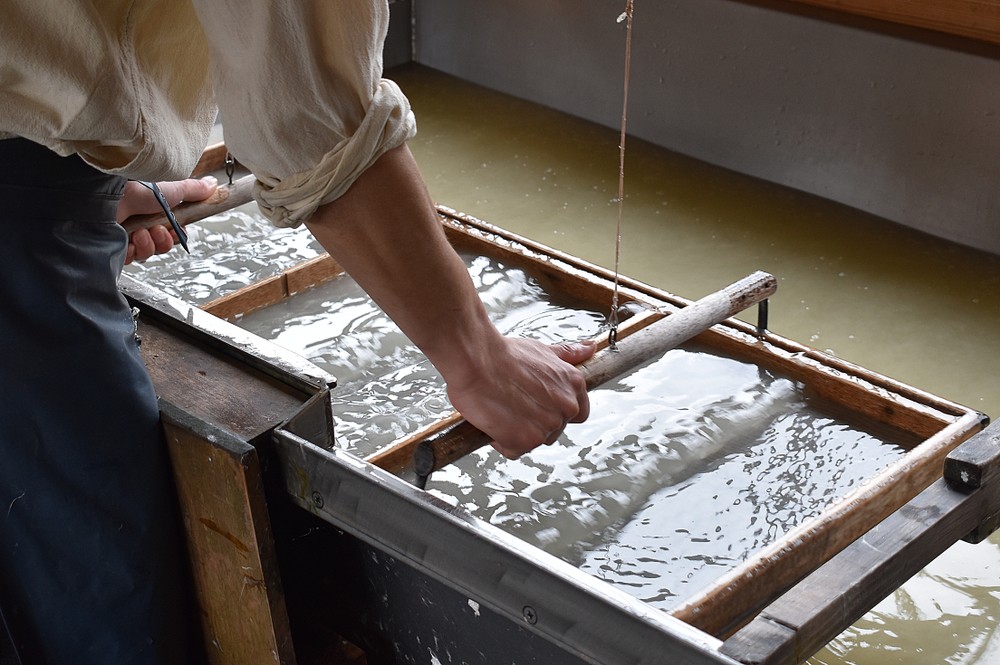
② Mino Washi (Gifu Prefecture)
- It is strong and durable
- Because it is made by the "Nagashi-suki" method, there are few unevenness in the paper surface
- It is used as a material for crafts such as Gifu lanterns and Gifu umbrellas
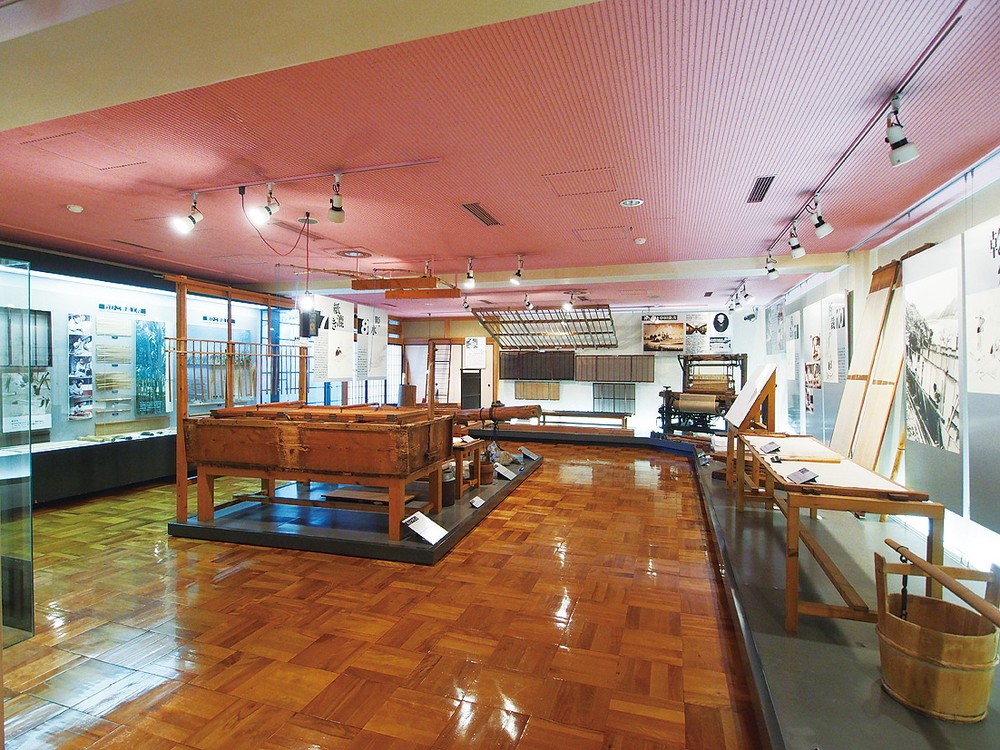
③ Tosa Washi (Kochi Prefecture)
- It is blessed with high-quality raw materials and highly transparent water
- It has a wide variety, and about 300 types are still being produced
- It is thin and durable. The ones used for the restoration of ancient documents and works of art are only 0.03-0.05mm
Japanese Paper Registered as UNESCO's Intangible Cultural Heritage
The "Washi - Japanese Handmade Paper Making Technique" was registered as a UNESCO Intangible Cultural Heritage in 2014. Among the numerous types of washi across Japan, three were selected: "Sekishu Banshi", "Hon Mino Paper", and "Hosokawa Paper". The common points among these three are mainly the following:
- Only "Kozo" is used as the raw material
- No bleaching with chemicals is done, so it becomes whiter over time
- The uniquely Japanese "Nagashi-suki" technique is used
How Washi is Made
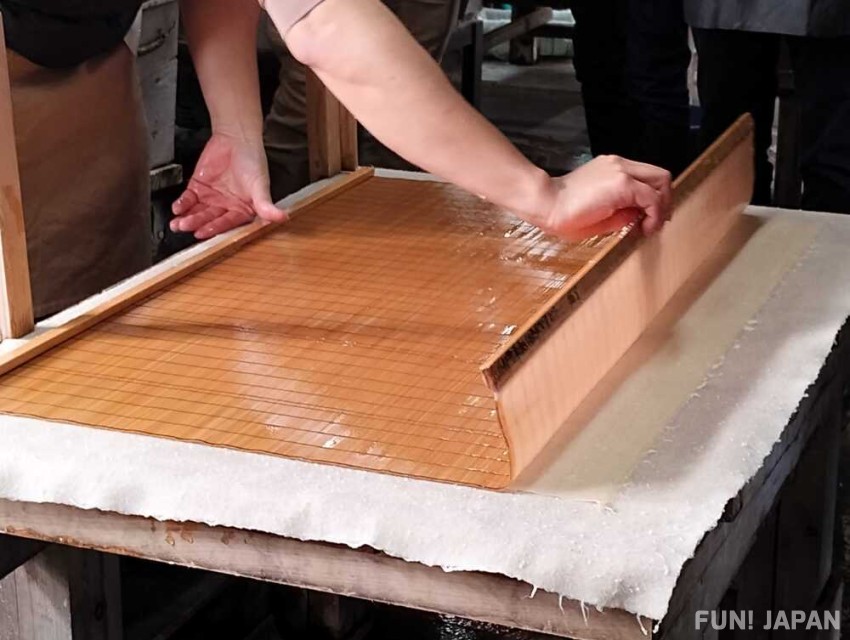
The process of making washi is complex and varies by region, but it can be mainly divided into three stages: raw material processing, raw material manufacturing, and hand papermaking.
① Process of treating raw materials: Harvesting of Kurokawa, Kurokawa removal, peeling
Kozo is harvested in November or December and cut to a length of 1.2m. It is steamed to make the bark easier to peel, and then peeled off all at once. The peeled Kurokawa is dried and stored in bundles of 15kg.
When it gets warm, the dried bark is soaked in water to soften it, and the Kurokawa is removed. The bast consists of Kurokawa, Aokawa, and Shirokawa, and in the case of high-quality paper, the Aokawa part is also carefully scraped off with a knife, and the Shirokawa is stored in a cool, dark place after drying.
② Process of manufacturing raw materials: aging, dust removal, beating
Before aging, the Kozo is soaked in water to soften the fibers and improve the penetration of the aging agent. After washing, the fibers are cooked with a aging agent using lime, soda ash, and caustic soda.
After aging, impurities are separated, so the material is left for a day, then soaked in running water to remove non-fibrous substances. Next, dusting is done by hand, removing any damaged or discolored parts. The dusted material is then beaten by hand or machine, separating the bundled fibers.
③ Papermaking process: Nagashi-suki/Tame-suki, Pressing, Itabari
Nagashi-suki consists of three steps: "Kake-nagashi", "Choshi", and "Sute-mizu". First, a shallow amount of water is drawn, and the fibers are evenly spread over the entire surface of the su (bamboo screen) in the "Kake-nagashi" process, creating the surface of the paper. Next, a slightly deeper amount of water is drawn, and the su-keta (bamboo frame) is moved to entangle the fibers in the "Choshi" process, adjusting the thickness. Finally, the "Sute-mizu" process is performed, where the water on the surface of the su is discarded, and the paper is stacked face down.
On the other hand, Tame-suki is an ancient method, using short beaten fibers. Water containing the raw material is drawn only once, and the su-keta is shaken until all the water is drained. Drying is done by stacking the paper with sheets in between, or sticking it to a board.
The "paper floor" made of stacked damp paper is left overnight, and then the moisture is removed with a press. By gradually increasing the pressure and squeezing out the moisture over 6 hours, a paper with shrinkage properties can be made.
The paper after pressing is attached to a drying board and dried. The finish differs between natural drying and forced drying, and the finished paper is processed according to its use and is also used as an art material.
Why not try making Japanese paper in Japan?
Ogawamachi
Ogawamachi is located almost in the center of Saitama Prefecture, and the town, which is blessed with the grace of the Tsuki River flowing through the center of the town, is a town where traditional industries such as Japanese paper and sake brewing are thriving. Also, because it has a long history and culture, it is also called "Little Kyoto of Musashi".

【Ogawamachi Japanese Paper Experience Learning Center】
This building was constructed by Saitama Prefecture in 1936 as a research facility for Japanese paper, and is now a facility where you can experience hand-papermaking and view exhibits.
The courses you can experience here range from the beginner's "Introductory Course" to the "Full Experience Course" that spans 4 days, so it will satisfy not only beginners but also advanced users.
- Address: 226 Ogawa, Ogawa-machi, Hiki-gun, Saitama 355-0321
- Access: About 10 minutes on foot from "Ogawamachi Station" on the Tobu Tojo Line and JR Hachiko Line,10 minutes from "Arima Ogawa IC" on the Kanetsu Expressway
- Official Website: https://www.town.ogawa.saitama.jp/0000003753.html
Higashichichibu Village
Higashichichibu Village, located in the western part of Saitama Prefecture, is the only village in the prefecture. It has been known as the "Village of Washi (Japanese paper)" for a long time, and together with the neighboring Ogawa Town, it produces "Hosokawa Paper". The access from Tokyo to the village is about 90 minutes by car and about 110 minutes by train, so you can enjoy the village life while also going out to Tokyo.
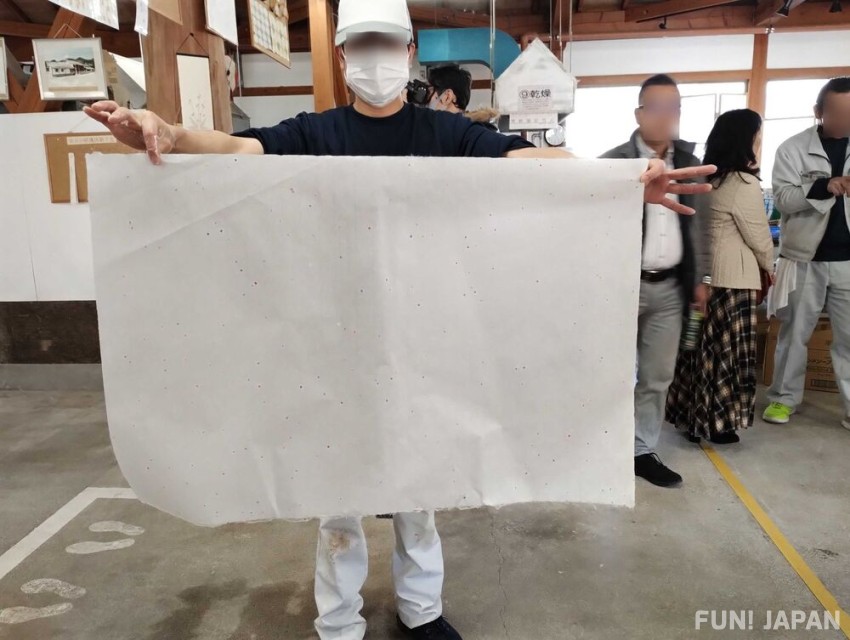
【Higashichichibu Village, Washi no Sato】
"Higashichichibu Village Washi no Sato" opened in 2016 as "Road Station Washi no Sato Higashichichibu", a facility where you can observe and experience the technique of making Japanese paper. It also has a direct sales store for agricultural products & specialty products, a soba noodle making workshop, and a food court, so you can enjoy meals and shopping.
- Address: 441 Ondo, Higashichichibu Village, Chichibu District, Saitama 355-0375
- Access: About 20 minutes by "Eagle Bus" from Ogawamachi Station on the Tobu Tojo Line
- Official Website: http://www.higashichichibu.jp/hosokawashi/washinosato
Klook's Japanese Paper Making Experience & Learning Tour
Visiting the birthplace of Washi and experiencing the local history and culture is one way to enjoy it, but for those who want to casually experience Washi making in Tokyo, why not join the tour below?
👉【klook】Japanese Paper "Washi" Making Experience in Asakusa
Light and durable! How about bags and accessories made of Washi?
When we say "Washi", it brings to mind a simple and traditional material, but in recent years, accessories, wallets, and bags made of Washi have been gaining popularity as stylish and environmentally friendly items.
With its unique features such as texture and flexibility intact, the special coating makes it worry-free from getting wet and tearing, making its "long-lasting" aspect also attractive.
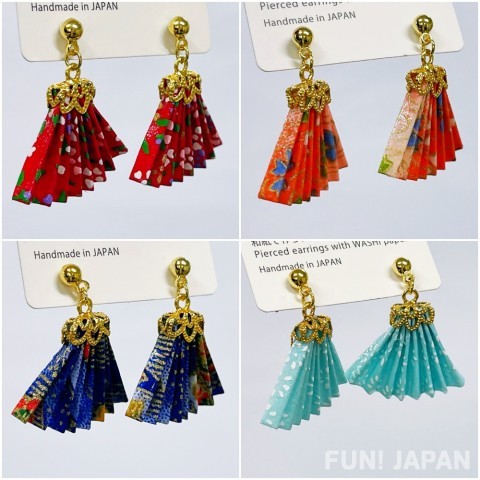
Washi Earrings
👉【FUN! JAPAN SELECT SHOP Recommended Products】
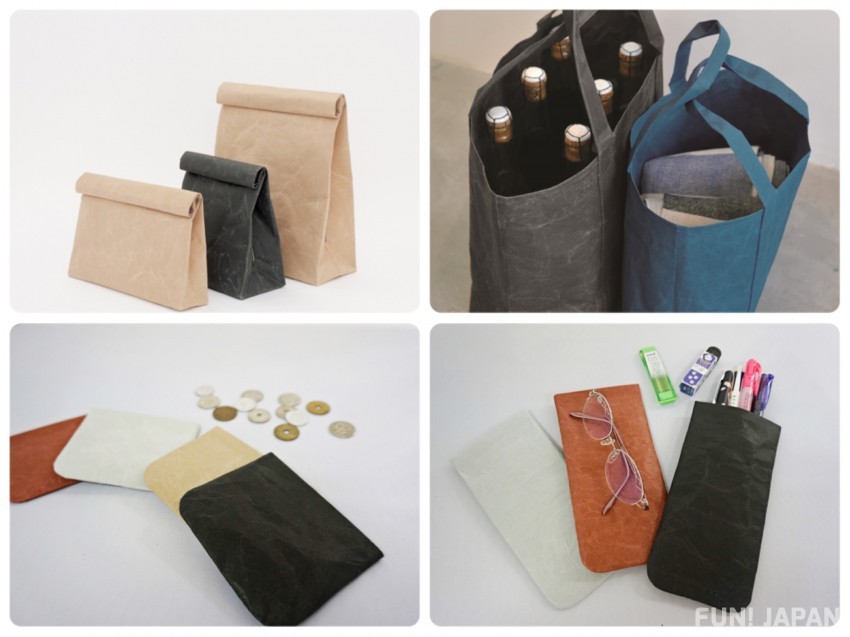
SIWA Bag
👉【FUN! JAPAN SELECT SHOP Recommended Products】
- 【Japanese paper】SIWA Clutch Bag (Wide)
- 【Japanese paper】SIWA Briefcase (M)
- 【Japanese paper】SIWA Tote Bag (M)
- Using the new material "Naoron" that inherits the technology of Japanese paper- "SIWA Ultra-lightweight PC Tablet Case Bag"
Washi, a type of Japanese paper, is not only an excellent material for various products but also for recording media. However, with changes in lifestyle, its production is decreasing year by year, and the problem of "lack of successors" faced by many traditional craft industries is also occurring. In order for the culture of Washi to be passed on to future generations, we encourage you to purchase Washi products and participate in Washi-making experiences to fully appreciate its charm.
Comments